Rådgiver
Teksten forneden er maskineoversat fra den tyske originaltekst.
Værd at vide til Siemens Simatic S7
Hvad er Siemens Simatic S7?
Hvordan er PLC-controlleren opbygget?
Købekriterier for SPS-controllere
Hvad udmærker Siemens Simatic S7 controlleren?
Hvilket S7-system til hvilket formål?
Hvad er Siemens Simatic S7?
Siemens Simatic S7 er en SPS-controller. PLC står for Lagerprogrammerbar styring. På engelsksproget område er disse enheder kendt som Programmable Logic Controller (kort PLC). En PLC-controller indsættes til styring og regulering af en maskine eller et anlæg, for eksempel i industrien til styring af transportbånd. Controlleren programmeres digitalt for at kunne betjene den maskine, der skal styres, med software-logik. En programmerbar styring fungerer altså ved hjælp af software, mens en almindelig programmeringsprogrammering styring (VPS) styrer periferienheder fast forbundet via relæer og kontaktorer. I modsætning til VPS er en PLC meget dynamisk og kan tilpasses individuelt til det pågældende anvendelsesscenarie uden at skulle ombygges mondages. En SPS har et fast installeret operativsystem og kan indlæse skrevne programmer via et hukommelsesinterface.
Hvordan er PLC-controlleren opbygget?
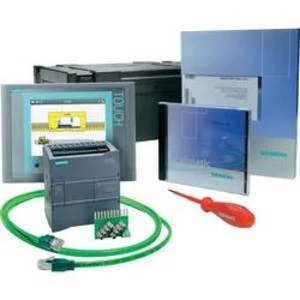
En SPS-controller har som regel indgange til sensorer og udgange til de såkaldte aktuatorer. Ved hjælp af indlæsningsværdierne, som forsyner sensorerne med PLC-controlleren, styres aktuatorerne via CPU-enheden på SPS-controlleren. F.eks. kan vinduer åbnes, når en bestemt temperatur er nået, eller transportbånd kan sættes i gang, hvis der er en vis vægt. Ved hjælp af analoge digitale omformere (ADU) kan ikke kun signaler fra digitale, men også fra analoge sensorer behandles. Analoge udgangskonstruktioner kan styres via digitale analoge konvertere (DAUs).
Dagens PLC-controller forsynes via en forsyningsspænding på 24 volt jævnstrøm. CPU'en er PLC-controllerens centrale beregningsenhed og omfatter ud over processoren de nødvendige lagringsområder til firmware og databearbejdning.
Selv om der findes en standard for PLC-controllere, IEC 61131, overholder de fleste PLC-systemer ikke strengt, så systemer fra forskellige producenter er normalt ikke kompatible med hinanden.
En SPS-controller har som regel indgange til sensorer og udgange til de såkaldte aktuatorer. Ved hjælp af indlæsningsværdierne, som forsyner sensorerne med PLC-controlleren, styres aktuatorerne via CPU-enheden på SPS-controlleren. F.eks. kan vinduer åbnes, når en bestemt temperatur er nået, eller transportbånd kan sættes i gang, hvis der er en vis vægt. Ved hjælp af analoge digitale omformere (ADU) kan ikke kun signaler fra digitale, men også fra analoge sensorer behandles. Analoge udgangskonstruktioner kan styres via digitale analoge konvertere (DAUs).
Dagens PLC-controller forsynes via en forsyningsspænding på 24 volt jævnstrøm. CPU'en er PLC-controllerens centrale beregningsenhed og omfatter ud over processoren de nødvendige lagringsområder til firmware og databearbejdning.
Selv om der findes en standard for PLC-controllere, IEC 61131, overholder de fleste PLC-systemer ikke strengt, så systemer fra forskellige producenter er normalt ikke kompatible med hinanden.
Købekriterier for SPS-controllere
Vigtige egenskaber ved køb af en PLC-controller er:
- Cyklustid: Angiver tiden til afvikling af en cyklus, herunder alle kommunikationsopgaver, der opstår. En cyklus består af CPU'ens startrutine, indlæsning af alle indgange og dermed også data fra sensorerne, der ligger der, seriel bearbejdning af programinstruktioner, skrivning af programresultater til controllerens Merker- og dataområder og styring af udgangsgrupper eller aktuatorer. CPU'en afbryder normalt en cyklus, hvis den varer for længe, hvilket f.eks. kan være tilfældet, hvis det program, der skal gennemføres, er dårligt skrevet.
- Reaktionstid: Reaktionstiden angiver tidsrummet mellem ændringen af et indgangssignal og reaktionen ved at ændre udgangssignalet. Den viser altså, hvor hurtigt aktuatorerne, der er tilsluttet til PLC-controllerens udgange, kan reagere på nyligt målte værdier for sensorerne.
- Merkeriens størrelse: Merkeriområdet er beregnet til opbevaring af foreløbige resultater. En markør skal indeholde data i formaterne bit, byte, WORD eller DWORD. Jo større området er, jo flere data kan gemmes der. Det påvirker hastigheden af cyklusbehandlingen og medfører for de fleste programmer en lavere cyklustid.
- Betjening af HMI: HMI står i denne forbindelse for Human Machine Interface og realiseres i dag ofte i form af en touchscreen. Simatic S7 systemet tilbyder et avanceret system med forskellige paneler med widescreen-skærme i størrelserne 4, 7, 9 og 12 tommer. HMI-systemerne kan i kombination betjenes både ved hjælp af knapper og med touch-indtastning. Derudover kan du via et USB-interface tilslutte mus, tastaturer og stregkodescannere og overføre data til et USB-stik.
- Skalerbarhed på SPS-systemet: Siemens giver med sine mange udvidelses- og styremoduler et skalerbart system, der uden større besvær kan monteres via hatskinnesystemet.
- Godkendelse af SPS-systemet: Opfyldelse af nationale og internationale standarder i SPS-systemet får stadig større betydning. Disse omfatter bl.a. cULus-, FM-, ATEX-, CE- samt en 61000-6-4, 60068-2-X og 61131-2
Hvad udmærker Siemens Simatic S7 controlleren?
Software og reservedele
Siemens Simatic S7 er den mest kendte og mest udbredte SPS. I den ældre serie S7-200 leveres controlleren med softwaren Step7MicroWin, i serierne S7-300 og S7-400 med de gængse software Step7. Efterfølgeren til S7-300-serien, der stadig er til rådighed op til 2020, er allerede klar med S7-1500-serien. Til S7-300 vil der stadig være en reservedelstilsikring 10 år efter produktionsstop.
Særlige kendetegn:
Fra S7-400-serien kan signalgrupper trækkes under spænding og tilsluttes (hot-swapping). Udvidelser af anlæg og komponentudvidelser er dermed mulige under drift.
Siemens S7-systemet udmærker sig ved en meget høj kapacitet til i/A-periferi, blandt andet fordi man kan skalere CPU-effekten dynamisk fra S/7-400-serien. Du kan bruge flere CPU'er i en enkelt centralenhed. Dette giver mulighed for at tildele enkelte komplekse aktiviteter, såsom styring, regning eller kommunikation, til hver CPU'er, hvilket giver en optimering af processortiden. Det fører til en bedre ydeevne under høj udnyttelse.
Desuden er en effektiv projektering og diagnose af programmeringsarbejde mulig takket være SIMATIC Engineering Tools. Dette tilbyder forskellige sprog som SCL samt grafiske engineering værktøjer til processtyringer, tilstandsgrafer og teknologiplaner.
Med Siemens-egenet multipoint-interface MPI (multipoint-interface) er det desuden muligt at overvinde store afstande inden for datakommunikation. Der kan kobles mellem to MPI-deltagere op til ni repeatere.
Programmering;
I modsætning til normen IEC 61131 skal man ved Siemens Simatic S7 adressere globale data som programmerer. Der er forskellige hukommelsesområder til rådighed. Desuden integreres input- og udgangssignaler ikke ved at deklarere variabler på adresser, men ved at sætte tal på PAE's og PPA's sagsomkostninger sammen med Operanerne E og A og deres adresser. I modsætning til PLC-systemer, der følger IEC 61131-standarden, spiller variabeldeklarationen ved step7 altså næppe nogen rolle.
Hvilket S7-system til hvilket formål?
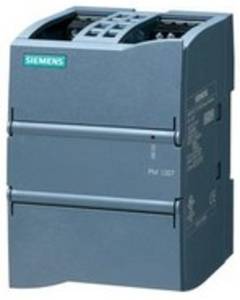
- S7 300: Til systemer med små styreenheder i det nedre og mellemstore effektområde. Dette omfatter f.eks. tekstilmaskiner, emballeringsmaskiner, generel maskin- og kontrolkonstruktion, værktøjsmaskinbyggeri, installationsteknik samt anvendelser fra elektroindustrien og elektriske håndværk.
- S7 400: Til det mellemstore og øverste effektområde. S7-400-serien udmærker sig ved muligheden for redundans af i i i i E/A-periferi. Dermed kan for eksempel udfald af en CPU, en PROFIBUS eller en signalbyggegruppe tolereres.
- S7 1500: Denne serie har omfattende integrerede Safety- og Security-funktioner. Hertil hører for eksempel en adgangskodebaseret know-how-beskyttelse mod uberettiget udlæsning og ændring af programmoduler samt en kopibeskyttelse mod kopiering af disse. Derudover findes der med denne serie for første gang et tilladelseskoncept med tilladelsesniveauer samt en beskyttelse mod manipulation af Engineering-data. Ethernet-forbindelser kan sikres med en integreret firewall og med udviklingen af VPN-forbindelser. Desuden er systemanalyse allerede integreret i CPU'en i denne serie. På denne måde stilles systemoplysninger direkte fra den centrale enhed og kan derefter udlæses på HMI, TIA-portal, via display eller via den integrerede webserver.